<< return to blog entries
2010-06-04 11:00:24 (9801 views) Full day at the plastic factory!! Very nice stuff...
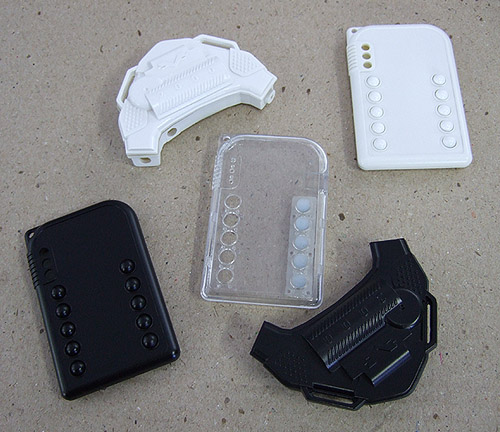
Polycarbonate prototypes... very nice finish for a machined part, although the new machine shop screwed up a few spots and we can't put the PCB in the receiver (but they are making a new piece free of charge to fix this).
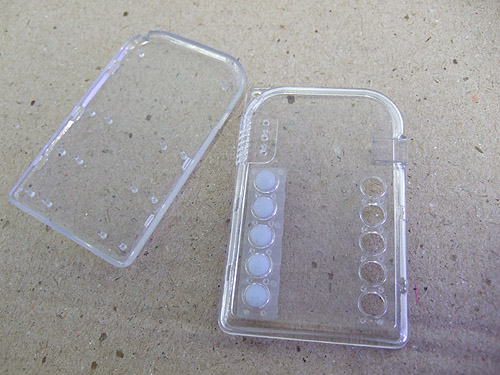
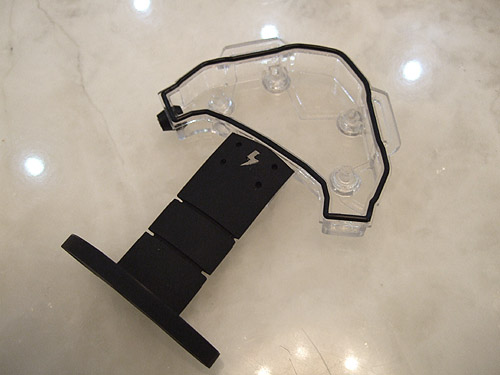
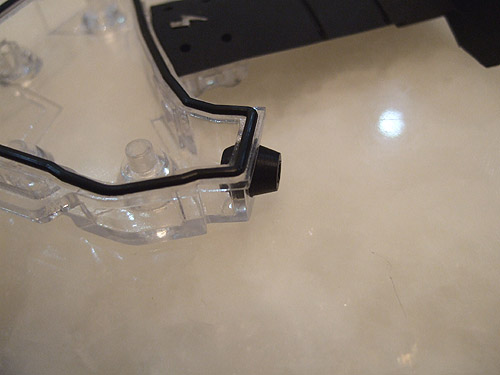
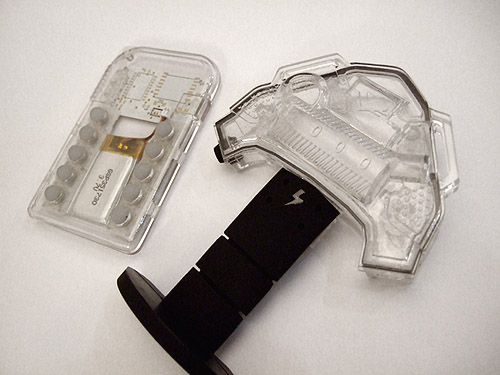
Now some spray painting... please note that these are machined prototypes; the molded parts will be even smoother and nicer. Still, these parts are Juicy! Very, very professional.
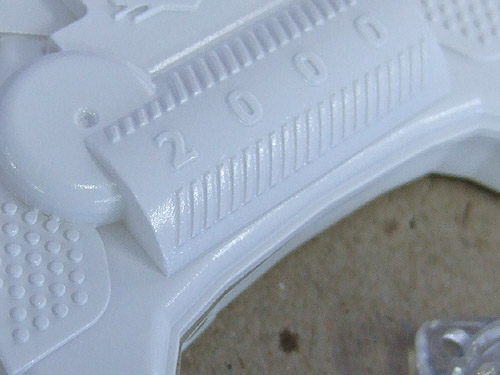
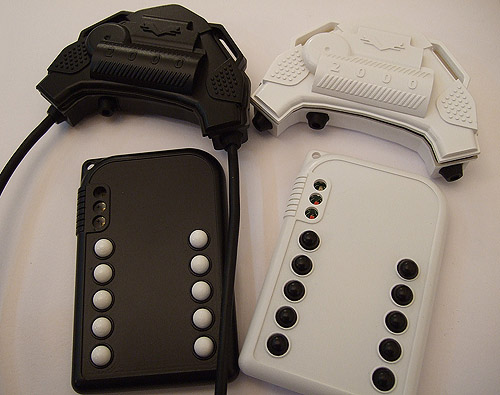
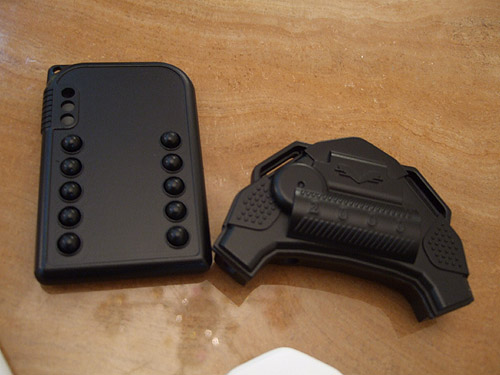
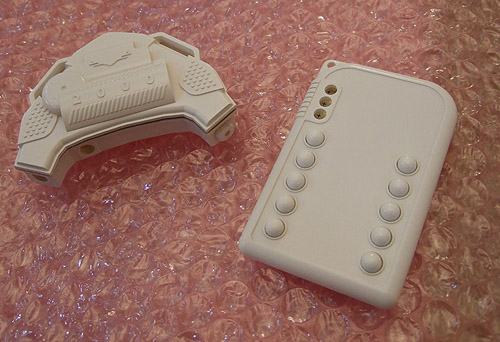

Ok... the "inside painting" trick didn't work very well - but the reason is very that these parts are machined, not molded. For Polycarbonate it makes a huge differences. Molded parts are extremely smooth, like glass, but machined parts - though clear - are not as smooth, they look more like candy than glass, and the sharp angles are opaque, and so the overall effect is not very good because (a) the surface isn't shiny enough and (b) the inner angles look "dirty". We won't see the real look of this until the mold's done...
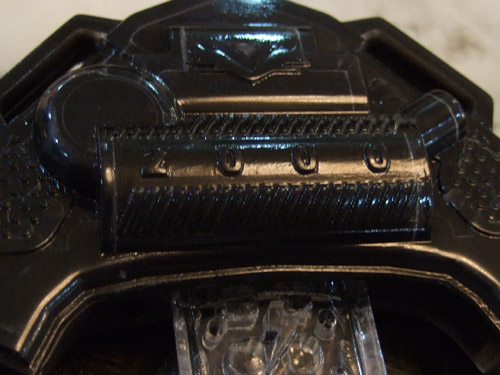
Despite this the remote came out looking respectable enough:
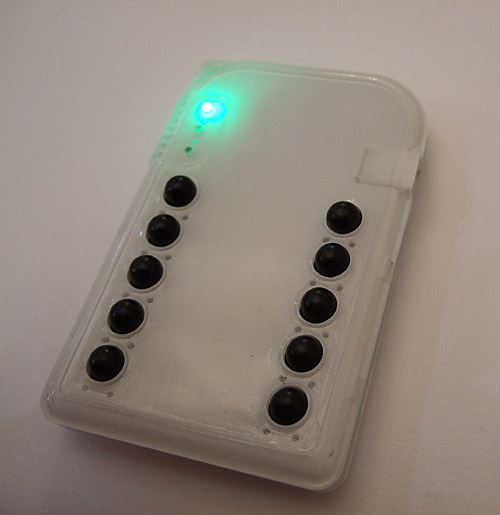
By the way, the USB connector fits in just right in the new enclosure.

A medium res shot here (click):
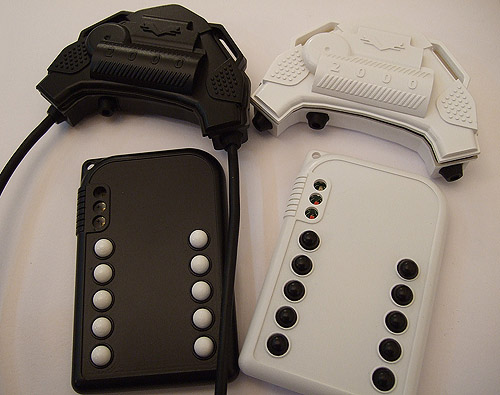
A high res shot here (click):
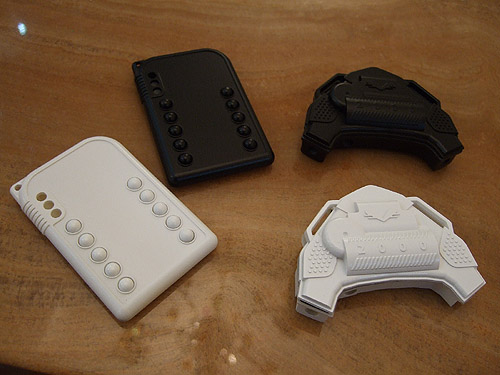
More notes and comments:
- the keypads are spray painted with a kind of spray paint that doesn't stick well to rubber. In the final version the rubber itself will be colored. But we like the shiny look, so we'll see what the rubber version looks like and possibly decide to spray paint them with the right paint (if a kind even exists that will both stick and produce this shiny look).
- Since we only had one prototype of the polycarbonate enclosures with the updated design, we sprayed our old prototypes. So the black and white remotes painted on the outside do not have the latest features (light pipe, USB connector hole). Similarly the receiver doesn't have the attachment boss at the bottom.
- Today we've also received the components needed to assemble the battery recharging remote control (now waiting only for the PCBs)
- Jason showed us some parts which we weren't able to find on the net on western sites: truly small brass inserts, perhaps only 2-2.5mm in diameter. If we can embed them into the top half of the receiver's enclosure, the screws will not need to touch the plastic directly, so the number of times you can open and close the receiver will be pretty much unlimited (as opposed to 10 or so). However this requires plastic modifications, OVERMOLDING (don't worry - Jason does it perfectly unlike you-know-who at the rubber factory), and CUSTOM SCREWS. So - unless we get seriously lucky this won't be in the first release for both timing and cost considerations. Now this impacts the mold, so we don't know for sure yet, but we have some chances of being able to offer just an alternative top half + screws at a later time (the bottom does not need to be changed). As you know we need to launch so we won't let this slow us down... but at least we'll find out exactly where we stand before going into production with the mold, and have an idea about whether we can do it right away, add them later, or nada.
More pictures may be found here until we have time to create some gallery code.
The plan:
- get PCBs, get new lower half of the receiver so we can fit the PCB in
- in the meanwhile we must finish the waterproofing tests with one spare non-painted transparent receiver enclosure top half (transparent parts allow us to test without having to open the enclosure every time to check for water). The unit is already 99.9% waterproof but we have some counter-intuitive watery behavior (capillary stuff) going on that requires insulation, heat shrink material, heat... and repeating the process many times to be sure it's something that can be done reliably in a production environment.
- assemble the very very final DL2000 prototype, make sure no problems exist *anywhere*, this will be the most comprehensive test batch ever and we need to finish all wireless reprogramming and USB reprogramming work by then, and make sure all the commented out code (timer mode, etc) has been reintroduced and works fine
- push the red button: go ahead with the plastic injection mold and do final EMC testing at the lab (need to brainstorm a bit about the correct sequence...). After these steps we will NOT be able to make any modifications whatsoever to the electronics or enclosures.
Comments
Post new comment
|
The outside-painted units definitely looked better -- but I would not want them. Outside paint will be subject to wear and tear and scratching.
So I have to say that I vote for colored plastic (though don't know how you'll do the LED shine-through).
I think the DL2000 itself would look very cool in clear plastic, so maybe that solves the problem. But the remote unit would look better in black, though I know people at DLLabs seem to prefer white. I think most of the posts on that topic preferred black remotes too.